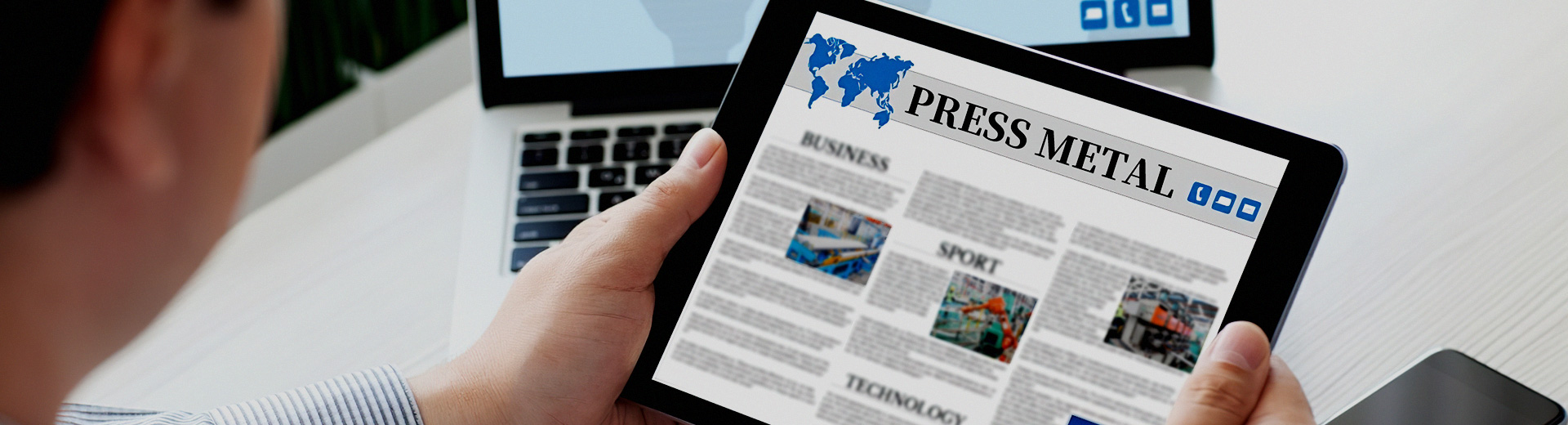
Lightweighting has been the primary issue in the automotive industry for years. This is the reason why engineers are rapidly adopting lightweight materials for chassis, body, interior, power train, and under-the-hood applications. No wonder the auto sector has made considerable strides in lightweighting in recent years, and it is the main focus of R&D efforts at automakers.
In fact, OEMs and suppliers are pushing to enhance multi-material vehicles that incorporate aluminum, high-strength steel, magnesium, carbon-fiber composites, titanium, and different kinds of foam, plastic, and rubber.?
Essentially, the main objective is to lessen overall vehicle weight to improve fuel economy and meet the ever-changing demands of increasingly electrified vehicle platforms. Still, the challenging part is to cost-effectively integrate different components while meeting stringent safety and ideals in performance. Let’s discuss more automotive lightweight manufacturing, particularly using aluminum alloy.
4 Main Automotive Lightweighting
Body lightweighting, powertrain lightweighting, chassis lightweighting, and interior and exterior trims lightweighting are the four main automotive lightweighting principles. Automobile lightweighting means lessening the overall mass of automobiles under the premise of ensuring the strength and safety performance of the body.?
Among them, the curb weight refers to the car’s weight once it is ready to run under normal conditions, including fuel with a fuel tank volume of 90%, spare tires, vehicle-included tools, and various oils and water.?
Surprisingly, the vehicle's fuel consumption decreases with reduced automobile mass, provided that other circumstances are the same. According to studies, for every 10% of a vehicle’s weight reduction, about 8% of the exhaust emissions, 6.8% of the fuel consumption, 8% of the acceleration time of 0-60km/h, and 5% of the braking distance can be eliminated.
Lightweight Materials in Automotive Lightweighting
Nowadays, the lightweight materials applied in the automotive sector are aluminum alloy, magnesium alloy, high-strength steel, and carbon fiber composite materials. But compared to all components used, the specific gravity of aluminum (2.7 g/cm3) is less than half that of steel (7.6 g/cm3) and copper (8.5 g/cm3). Thus, as an ideal lightweight material, the potential advantages of aluminum are becoming very apparent.
Generally, aluminum alloys and high-strength steels are the mainstream in material lightweighting. However, the process of lightweighting is mainly achieved through lightweight materials with specific methods. Currently, lightweighting can be accomplished in three ways:
By Lightweight Materials
The traditional ordinary steel structure are now replaced with the lighter structure of aluminum alloy, high-strength steel, magnesium alloy, or carbon fiber composite materials. Technically, the general trend is to replace standard steel with thermoformed steel, thermoformed steel with aluminum alloy, or aluminum alloy with carbon fiber while replacing some parts with engineering plastics.
By Lightweight Design??
This is achieved by enhancing new automotive architectures or optimizing body parts, even reducing engine parts size. For instance, the Buick Regal's rear suspension upper/lower arms were reduced weight through perforating.
By Lightweight Process
In practice, such as thermoforming, laser welding plate, and other processes, lightweight is achieved by using lightweight components with particular lightweight techniques to achieve weight reduction effects. For example, due to the denser material of the forged rim, the spoke structure is thinner and thinner, and the weight is naturally reduced.
So Why Choose Aluminum Alloy??
Magnesium alloys and carbon fiber materials have significant defects, which limits their large-scale commercial use. The shortcomings of magnesium alloys with poor corrosion resistance, flammability, and high cost limit their application, so magnesium alloys are generally used in interiors, wheel hubs, and powertrains.?
On the other hand, carbon fiber composites cost much more than magnesium-aluminum alloy. However, the weight reduction effect is far better than metal materials, and it is currently only used in racing cars, super sports cars, and the likes.
In the integrated production chain, like energy-saving and emission reduction, manufacturing costs, and recycling effects, aluminum alloys are far superior to other materials. Compared with high-strength steels, aluminum alloys have the following benefits:
Cost
Did you know that aluminum alloys are only 2.5 times the price of steel, which is similar to magnesium alloy but lower than carbon fiber composites? However, the corrosion problem of magnesium alloy hinders its large-scale application in the automotive sector.??
Hence, aluminum alloy is the best lightweight material at this stage. In terms of weighing strength and cost, the trend of aluminum developing into a mainstream automotive material is positive.
Performance
The density of aluminum is about 1/3 of steel so using 1 kg of aluminum can replace the steel with a self-weight of 2.25 kg in automobiles. We can say that the overall weight reduction effect is greater than 50%, plus, aluminum alloy has the advantages of high strength, recyclability, corrosion resistance, low density and so on.
Product Manufacturing
Thanks to the high plasticity feature of metals, the overall product performance has increased the structural properties of automobiles. Doing so can provide great potentials and cost advantages in converting pre-designed to finished products through engineering capabilities.
Other Special Features?
Aluminum alloy has low density, strong processability, and can be processed into various shapes and sizes according to the client’s specific needs, which, together with its price advantage, is the material of choice to realize the lightweighting of the whole vehicle. At present, the application of aluminum alloy in automobile is mainly based on aluminum plates.
Aluminum plates are generally applied for body coverings, such as door panels, wings, and more. Aluminum extrusion profiles are mainly used for interior and exterior structural parts, such as crash beams, subframes, door sill plates, instrument beam brackets, and the likes.
?